Presses come in many designs, varying from systems with only a few pots and suitable for primarily small-scale chocolate manufacturing, to presses fitted with twelve or fourteen pots that are used mostly in the cocoa industry, and even double presses that have combined cylinder bodies in the centre with pots and counterpots on both sides. Double presses are falling into disuse for a number of reasons.
Figure 3.1: Cocoa press (14 pots) (Duyvis)
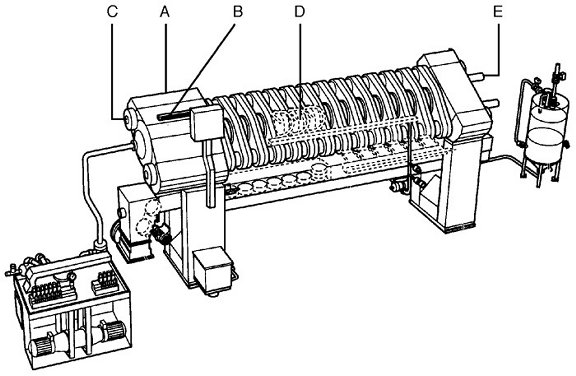
The 14-pot cocoa press consists of the following parts: A. cylinder body with main ram B. ruler C. columns D. filling circuits E. push-out cylinders
The two columns (C) connect the cylinder body (A) to the rear of the press, which is necessary for absorbing the huge force (well over 1450 tons) caused by the hydraulic pressure exerted by the main ram on the pots and counterpots.
The compressive force of the ram can be calculated as follows: compressive force = 2640 cm2 (ram surface area) x 550 bar (hydraulic oil pressure) = about 1450 tons.
Special constructions and materials have to ensure that the columns are resistant to wear due to the constantly changing loads to which they are subjected, thus making them the most vulnerable parts of the press.
The columns come in two basic designs, one fixed to both ends of the press by means of thread and nuts, while the other has forged heads that fit tightly in the cylinder body and the end part of the press. The forged-head type was designed to overcome the problem of crack formation in the cores of the threads due to metal fatigue.
The pot is in fact a thick metal plate with a large round polished hole, the press chamber. The counterpot is made of a slightly thinner metal plate and has channels through which the butter can be discharged. The counterpot has a cylindrical part mounted on one side of it that perfectly fits in and consequently slides smoothly in and out of the press chamber of the pot. The pot and counterpot together are called a set.
Figure 3.2: Pot and Counterpot system (Duyvis)
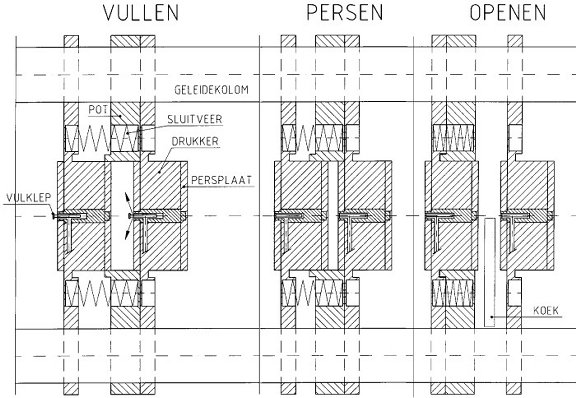
Pots and counterpots, or sets, are mounted alternately between the cylinder body and the rear part of the press. The columns act as guides to ensure that all the pots and counterpots slide smoothly in and out of each other. During the pressing process the pots are pressed against the flat sides of the counterpots of the adjoining set by means of retainer springs to keep the press chambers tightly closed.
Each counterpot has a pressing plate mounted on either side, i.e. a steel plate with fine grooves in the front side of the plate covered with a coarse-mesh filter screen made of steel wire, or a plate with perforations covered with one or two screens of a finer mesh. Because the steel wire of the screens may break, which could cause metal particles to fall into the product, the screens, at least the upper screen, should be made of magnetic material to enable the removal of metal particles by magnets before or after powder grinding.
Figure 3.3: Press plate (Duyvis)
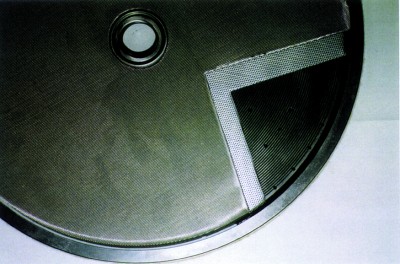
The pressing plate is perforated with small holes to connect the grooves in the front of the plate with the discharge channels at the back that lead to the butter discharge channels of the counterpots. This means that each press chamber, or pot, has outlets on two sides for the discharge of the butter via the counterpots.
The pressing plate is sealed by placing a felt cord between the pressing plate and the pot to prevent liquor flowing out during pressing.
The press is equipped with a liquor filling bar for feeding the product via special high-pressure hoses to the filling circuits.
There are two types of filling circuits. One system is mounted on the outside of the pots, whereas the other type is fitted centrally in the counterpots. Both filling circuits have a built-in non-return valve to prevent that after filling or during pressing, liquor or cake flows back from the press chamber through the filling circuit, which would cause clogging of the liquor feed system when the next pressing cycle starts.
The hydraulic pressure (500-550 bar) needed for the ram to be pushed out of the cylinder body, as well as for the pots and counterpots to be pressed together, is supplied by the hydraulic pump unit. This separate unit also supplies the pressure for the two hydraulic push-out cylinders that open up the press. These cylinders are mounted in the end part of the press and pass through all sets. Special supporting shafts or strips mounted on the pots and counterpots ensure that these all remain equidistant from each other when the press is opened.
The press is kept at a constant temperature of between 95-100°C by means of low-pressure steam or a proper heating medium.
|